We are pleased to welcome you to our blog. Here you will find useful information, applications, and guidance on the topics of automation, industrial sensors, and explosion protection.
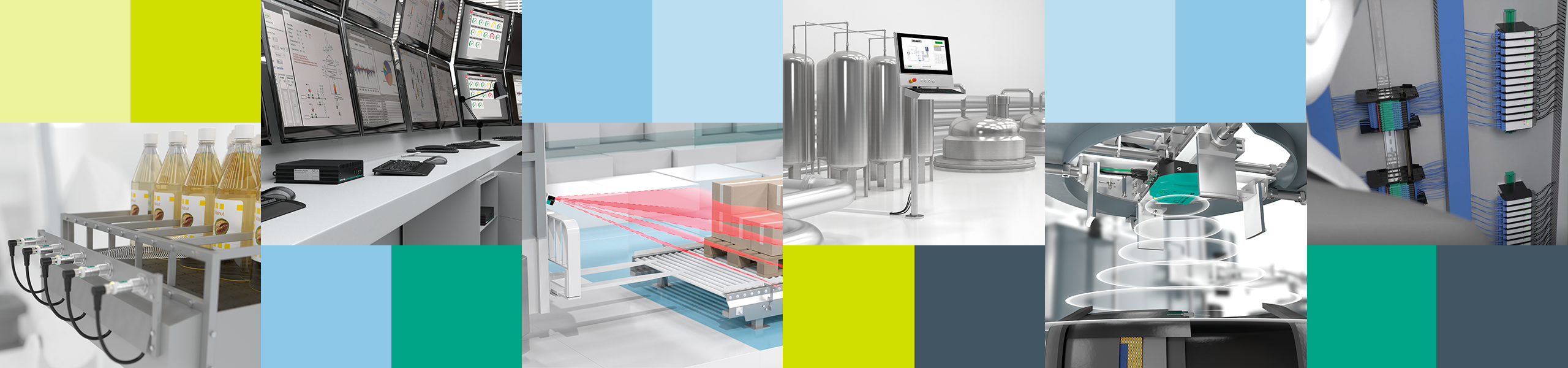
Welcome to our blog. Here you will find current articles on the topics of industrial automation and sensor technology.
Reliable Level Measurement—Why Two Different Technologies Are Crucial
Level measurement technology is the basis for reliable process control in the chemical, petrochemical, environmental, and other related industries. We explain why it is advisable to use a different principle of measurement for the probe and technology for continuous level measurement and level limit detection in critical tank level applications.
Frequently Asked Questions about Retroreflective Sensors and Reflectors
We answer the most frequently asked questions about the use of retroreflective sensors and what type of reflector is suitable for your application.
Four TCP-based Communication Protocols That Are Key to IIoT—Part 3: AMQP
Find out more about the key features of the interoperable asynchronous publish/subscribe communication protocols AMQP. We take a closer look at the interoperability, real-time behaviour, security, implementation, and typical applications of AMQP compared to MQTT.
Smart-Ex® 03 Intrinsically Safe Smartphone with All-Around USB-C Interface
The Smart-Ex 03 intrinsically safe, 5G-capable Android smartphone features the USB 3.1 Type-C standard interface and offers you a complete desktop experience via a multiport adapter. Learn more about the advantages the USB-C connector offers for your digital applications.
Four TCP-based Communication Protocols That Are Key to IIoT—Part 2: OPC UA
Tcp-based communication protocols enable smart communication all the way to the cloud. Learn more about the interoperability, real-time behavior, security, implementation, and application of OPC UA.
Four TCP-Based Communication Protocols That Are Key to IIoT—Part 1: MQTT
What is MQTT and how does it work? Learn all about the interoperability, real-time behavior, security, implementation, and applications of MQTT.
Subscribe to our newsletter and receive regularly news and interesting information around the world of automation.